What is Porosity in Welding: Key Elements and Their Effect On Weld High Quality
Understanding Porosity in Welding: Checking Out Causes, Results, and Prevention Strategies
As experts in the welding market are well aware, understanding the reasons, impacts, and avoidance techniques related to porosity is critical for accomplishing durable and trustworthy welds. By diving right into the origin causes of porosity, examining its harmful impacts on weld quality, and checking out efficient prevention techniques, welders can boost their understanding and skills to generate top notch welds regularly.
Usual Reasons of Porosity
Contamination, in the kind of dust, grease, or rust on the welding surface, creates gas pockets when warmed, leading to porosity in the weld. Incorrect shielding occurs when the shielding gas, commonly utilized in procedures like MIG and TIG welding, is incapable to totally shield the liquified weld swimming pool from responding with the bordering air, resulting in gas entrapment and subsequent porosity. Additionally, poor gas coverage, often due to wrong flow rates or nozzle positioning, can leave components of the weld unsafe, enabling porosity to form.
Impacts on Weld High Quality
The presence of porosity in a weld can significantly jeopardize the general high quality and integrity of the bonded joint. Porosity within a weld produces voids or tooth cavities that deteriorate the framework, making it extra susceptible to breaking, rust, and mechanical failure. These spaces function as stress and anxiety concentrators, lowering the load-bearing capacity of the weld and enhancing the probability of premature failure under used stress and anxiety. In enhancement, porosity can also function as possible sites for hydrogen entrapment, further intensifying the deterioration of the weld's mechanical properties.
In addition, porosity can impede the efficiency of non-destructive testing (NDT) strategies, making it challenging to discover various other flaws or stoppages within the weld. This can bring about considerable safety concerns, specifically in important applications where the structural integrity of the bonded elements is paramount.

Avoidance Techniques Summary
Provided the destructive effect of porosity on weld quality, reliable prevention strategies are critical to preserving the structural honesty of welded joints. One of the main prevention strategies is detailed cleaning of the base materials prior to welding. Pollutants such as oil, grease, corrosion, and moisture can add to porosity, so making sure a clean job surface is essential. Correct storage of welding consumables in completely dry problems is also essential to stop wetness absorption, which can result in gas entrapment throughout welding. Furthermore, choosing the ideal welding parameters, such as voltage, current, and travel rate, can help decrease the threat of porosity development. Guaranteeing adequate shielding gas circulation and coverage is an additional important prevention strategy, as not enough gas insurance coverage can lead to climatic contamination and porosity. Ultimately, appropriate welder training and qualification are essential for carrying out preventive steps properly and consistently. By including these avoidance techniques right into welding techniques, the occurrence of porosity can be considerably decreased, leading to more powerful and much more dependable welded joints.
Significance of Appropriate Shielding
Proper securing in welding plays a vital function in protecting against atmospheric contamination and making certain the honesty of bonded joints. Shielding gases, such as argon, helium, or a combination of both, are commonly used to safeguard the weld swimming pool from reacting with elements airborne like oxygen and nitrogen. When these responsive aspects come into call with the warm weld pool, they can create porosity, leading to weak welds with decreased mechanical homes.

Insufficient shielding can lead to various flaws like porosity, spatter, and oxidation, compromising the architectural honesty of the bonded joint. Therefore, sticking to correct securing techniques is necessary to generate top quality welds with marginal defects and make certain the longevity and reliability of the bonded elements (What is Porosity).
Monitoring and Control Methods
Just how can welders effectively keep an eye on and control the welding procedure to make certain ideal results and avoid problems like porosity? By constantly monitoring these variables, welders can recognize variances from the optimal problems and make immediate changes to protect against porosity development.

In addition, executing correct training programs for welders is necessary for keeping track of and controlling the welding process successfully. What is Porosity. Educating welders on the Related Site significance of see this website preserving regular criteria, such as correct gas protecting and travel speed, can aid protect against porosity issues. Routine assessments and accreditations can also make sure that welders excel in monitoring and controlling welding processes
Additionally, using automated welding systems can improve tracking and control capacities. These systems can exactly manage welding criteria, minimizing the possibility of human mistake and guaranteeing regular weld high quality. By integrating advanced monitoring innovations, training programs, and automated systems, welders can efficiently monitor and manage the welding process to minimize porosity issues and accomplish high-quality welds.
Verdict
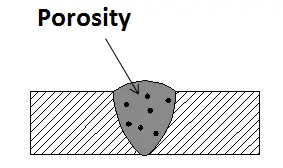